Fire Brick Fireclay Bricks Insulating Clay Tile | Wedge India
Fire bricks, also known as refractory bricks, are specialized bricks designed to withstand high temperatures and harsh conditions. They are commonly used in applications that involve extreme heat, such as fireplaces, furnaces, kilns, and industrial ovens.
Fire brick is heat-resistant brick, refers to a type of brick specifically designed to withstand high temperatures and harsh conditions.
Get good quality, long life, more durable, high performance low price Fire Brick, Fire Clay Bricks, Chamotte Bricks, Insulating Bricks for Kiln, Furnace, Oven, Dryers, Blast Furnace, Hot Stoves, Boilers, Ladle Safety Linings, Torpedo Ladles, Pizza Ovens etc. at Wedge India.

Features of Wedge Fire Clay Bricks
Fire brick is high temperature resistant refractory product with Al2O3 content of 30%-50%. Fire brick is made of Fire Clay and also known as Fire Clay Brick. Fire clay bricks can resist the erosion of acid slag and acid gas; have good thermal performance and can withstand rapid cooling and rapid heating. The fire clay bricks are mainly used for heat boiler, glass kiln, cement kiln, chemical fertilizer gasification furnace, blast furnace, hot blast furnace, coking furnace and electric furnace. Fire Clay Bricks have high fire resistance, high density, low porosity, excellent creep performance at high temperature and good bulk stability. Fire clay is commonly found beneath coal seams and is used to make fire bricks. Fire clay has two major constituents: silica and alumina, with silica ranging from 60 to 70% and alumina ranging from 25 to 35%.
Here are some key Features of Fire bricks:
-
Composition: Fire bricks are typically made from ceramic materials that have a high resistance to heat. The primary component is usually fire clay, which is a type of clay that can withstand high temperatures without deforming or cracking. Other additives such as silica, alumina, and other refractory materials may be included to enhance the properties of the bricks.
-
Heat resistance: Fire bricks are capable of withstanding temperatures ranging from 1,200°C (2,192°F) to 1,800°C (3,272°F) and higher, depending on the specific type and composition. They are engineered to retain their structural integrity and insulation properties under extreme heat.
-
Insulation properties: Fire bricks have excellent insulation properties, which means they can effectively retain heat within an enclosure while preventing the transfer of heat to the surrounding environment. This makes them ideal for lining the inner walls of furnaces, kilns, and other high-temperature equipment.
-
Types of fire bricks: There are different types of fire bricks available, each with specific properties and recommended applications. Some common types include:
-
Dense fire bricks: These bricks have a high density and low porosity, providing excellent strength and resistance to abrasion. They are suitable for applications that require high mechanical strength, such as industrial furnaces.
-
Insulating fire bricks: These bricks have a lower density and higher porosity, making them more effective at insulating against heat. They are often used in applications where reducing heat loss is crucial, such as in the walls of kilns or fireplaces.
-
Acid-resistant fire bricks: These bricks have additional additives to resist chemical corrosion, making them suitable for applications that involve acidic or corrosive environments.
-
-
Installation: Fire bricks are typically laid in a specific pattern using refractory mortar, which is designed to withstand high temperatures. The bricks should be tightly fitted and secured to ensure a solid and durable structure.
-
Maintenance: Fire bricks are durable, but they may eventually deteriorate over time due to thermal cycling, chemical exposure, or mechanical stress. Regular inspections and maintenance are important to identify any damaged bricks and replace them to maintain the integrity of the structure.

Fire brick is a type of refractory brick, tile or a block made of ceramic materials used in lining furnaces, kilns, fireboxes, and fireplaces. Fire bricks are manufactured to withstand high temperature and usually have a low thermal conductivity for greater energy efficiency. Dense firebricks are used in applications with extreme mechanical, chemical, or thermal stresses, such as the inside of a wood-fired kiln or a furnace, which is subject to abrasion from wood, fluxing from ash or slag, and high temperatures. Higher porosity Fire bricks can be used in less harsh working conditions such as in an electric- or natural gas-fired kiln, these are known as "kiln bricks". These types bricks have lesser strength but they are much lighter and easier to form and insulate far better than dense bricks.

How to Make Fire Bricks
Principal raw materials for manufacturing of firebricks are fireclays, hydrated aluminum silicates, minerals of high aluminum oxide content, such as bauxite, and kyanite and sources of silica, including sand and quartzite; magnesia minerals, magnesite, dolomite, forsterite, and olivine; chromite, a solid solution of chromic oxide with the oxides of aluminum, iron, and magnesium; carbon as graphite or coke; and vermiculite mica. Minor raw materials are zirconia, zircon, thoria, beryllia, titania, and ceria, and other minerals containing rare-earth elements.
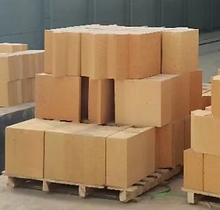
Types of Fire Bricks
There are several types of fire bricks available, each with its own characteristics and recommended applications. Some common types include:
-
Dense fire bricks: These bricks have high density and low porosity, providing excellent mechanical strength and resistance to abrasion. They are suitable for industrial furnaces and other applications that require high durability.
-
Insulating fire bricks: These bricks have lower density and higher porosity, offering superior insulation properties. They are commonly used in the walls and roofs of kilns, ovens, and furnaces to minimize heat loss.
-
Acid-resistant fire bricks: These bricks have additional additives to resist chemical corrosion, making them suitable for environments with acidic or corrosive conditions.
Technical Properties of Fire Bricks
-
Low thermal conductivity and high energy efficiency.
-
High mechanical strength.
-
High thermal resistance up to 1500 Degree C.
-
Lower cost in comparison with alternate materials.
-
High chemical resistance.
-
High thermal shock resistance.
-
Low shrinkage at high temperature.
-
High compressive strength.
-
High insulation performance.
-
Resistance to high temperatures.
-
Resistance to temperature fluctuations.
-
Pressure resistance at higher temperatures.
-
At higher temperatures lower expansion.
-
Ability to resist reduction or oxidation.
-
High abrasion resistance to dust, metal, slag, etc.
-
Low thermal absorption at high temperatures.
-
Consistency in size, shape, and composition.

Applications of Fire Bricks
Fire clay bricks are typically used as linings for kilns, furnaces and boilers they possess mechanical strength and can be subjected to extreme thermal cycling and thermal shock. Fire clay bricks also have a high thermal mass which ensures they retain heat and provide excellent energy efficiency. Fire bricks are used to construct kilns, furnaces, and fireplaces. Fire bricks find applications in various industries, including:
-
Fireplaces and stoves: Fire bricks line the interior of fireplaces, wood-burning stoves, and chimneys to protect the surrounding structure from heat and prevent damage.
-
Industrial furnaces and kilns: Fire bricks line the inner walls of high-temperature furnaces, kilns, and boilers to withstand extreme heat and ensure efficient heat retention.
-
Foundries and metalworking: Fire bricks are used in foundries and metalworking facilities to construct furnaces and crucibles for melting and shaping metal.
-
Glass manufacturing: Fire bricks are employed in glass kilns and furnaces to withstand the high temperatures required for glass production.
-
Furnace construction
-
Blast furnace ⁄ Hot blast stove
-
Steel foundries
-
Furnace in the nonferrous metal industry
-
Coke oven and Gas furnace
-
Glass industry
-
Cement industry
-
Safety lining of ladle
-
Backup lining of boiler

HS Code, GST HSN of Fire Clay Bricks is 69029010
Technical Properties of Low Alumina Fire Clay Bricks | Low Price
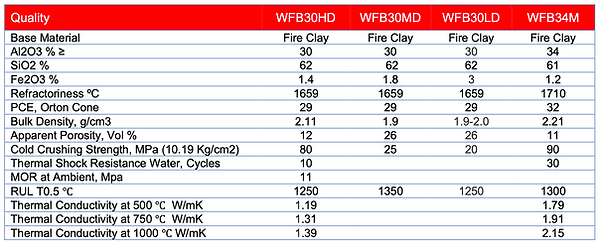
Technical Properties of High performance Fire Bricks | Medium Price

Technical Specifications of High Duty Fire Bricks | High Price

Technical Properties of Chamotte Bricks

WETON | Insulating Fire Brick
High Strength | High Insulation | Low Cost
WETON are lightweight high refractory insulating fire bricks most suitable for high temperature insulation up to 1600 Degree C. These bricks are produced from high purity raw materials to achieve lowest possible thermal conductivity without compromising on mechanical strength.
Feature & Advantages
• Low thermal conductivity at high temperatures
• Low bulk density, thus low heat storage
• Good high temperature resistance
• Reduced thermal shrinkage
• High thermal shock resistance
• High mechanical resistance
Applications
• Insulating layer in torpedo ladles
• Ceramic industry plants like chamber,
• Bogie hearth and tunnel kilns
• Anode baking furnaces
• Cracker and process plants
• Combustion chamber lining
• Insulation in reheating furnaces
• Walking beam furnaces
• Rapid roller kilns for cement
• Glass furnaces & Tunnel furnaces

Insulation U R Value Heat Loss Calculator
Right Insulation Materials Selection to get most feasible commercial solution. Achieving right combination of Insualtion materials and thickness is most complex decision to achieve lowest heat loss with minimum insulation thickness at various applications and temperatures. Wedge India helps its client to select right combination of Insulation material for various applications based on R Value heat loss calculator software, u p k calculations to find right insulation thickness, achieve target cold face temperature, and minimise heat losses at very low price. We also make energy audits as per requests from our customers. R value calculator delivers best insulation thickness r30 r38 r19 r49 r21 r60 for home and buildings to save cost at high efficiency.
Get Thermal Calculation, Insulation Thickness, Heat Loss
Benefits of Heat Loss Calculator
-
Get right Thickness of Insulation.
-
Find right Insulation Materials Selection.
-
Get lowest cost combination of Insulation System.
-
Get better heat loss reduction decision.
-
Clear view of Energy Saving potential and Energy Audits.
-
Low cost and optimum Furnace Design.
-
Best Energy cost reduction possibilities.